VisiConsult Enhances Customer Support with On-Site Machine Data Monitoring
As a specialist in X-ray inspection solutions, VisiConsult often faces the challenge of unclear root causes when handling support requests. This leads to time-consuming diagnostics and potentially extended downtime. By capturing key machine parameters from on-site machines and transmitting them to a custom software solution built with Heisenware, alarms are automatically analyzed, and the data is visually presented. Service technicians instantly receive all the necessary information, significantly reducing response times for support inquiries.
About VisiConsult
Die VisiConsult X-ray Systems & Solutions GmbH is a leading provider of non-destructive X-ray inspection solutions, based in Stockelsdorf near Lübeck, Germany. The company offers custom systems for non-destructive testing (NDT), primarily used in quality assurance. With over 25 years of experience in image processing and industrial X-ray technology, VisiConsult operates globally and is renowned for its innovative solutions. Employing around 250 people, VisiConsult provides industry-spanning applications as well as specialized systems for electronics manufacturing and electric vehicle battery inspection. Through ongoing research and development, the company continues to set new standards, helping customers improve both efficiency and quality.
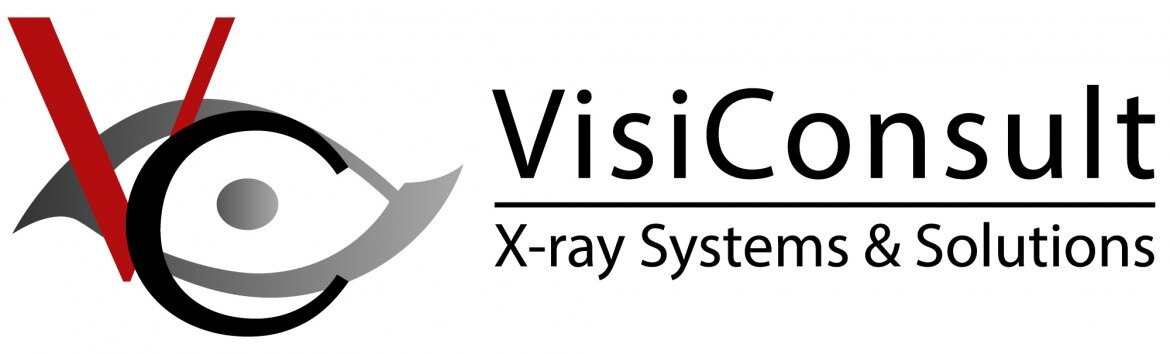
Lack of Clear Information and Lengthy Diagnostics
Quick action is essential when it comes to support requests, especially to minimize downtime. Customers often report issues over the phone, but the information they provide about the machines and the problems is typically vague. This makes it difficult for the service team to take targeted action. Key machine parameters are often missing, delaying problem identification and prolonging downtime. Additionally, the customer contacts are increasingly unfamiliar with the software and equipment, further complicating communication. In many cases, the only option left is to remotely access the machine’s control PC, a time-consuming process for analyzing and resolving the issue.
Automated Data Collection and Analysis Through a Low-Code Custom Software
VisiConsult now uses a custom software solution built with Heisenware that automatically collects and analyzes key machine parameters. Every hour, CSV files are generated on the machine’s control PCs and securely transmitted to the cloud via MQTTS, using the Heisenware Agent. After successful transmission, the agent deletes the files to prevent duplicate uploads.
Once in the cloud, the data is processed and fed into a service dashboard. This dashboard provides an overview of all alarms with acknowledgment options, live views of recently transmitted parameters, and a historical view that allows specific machine analysis through a drop-down menu.
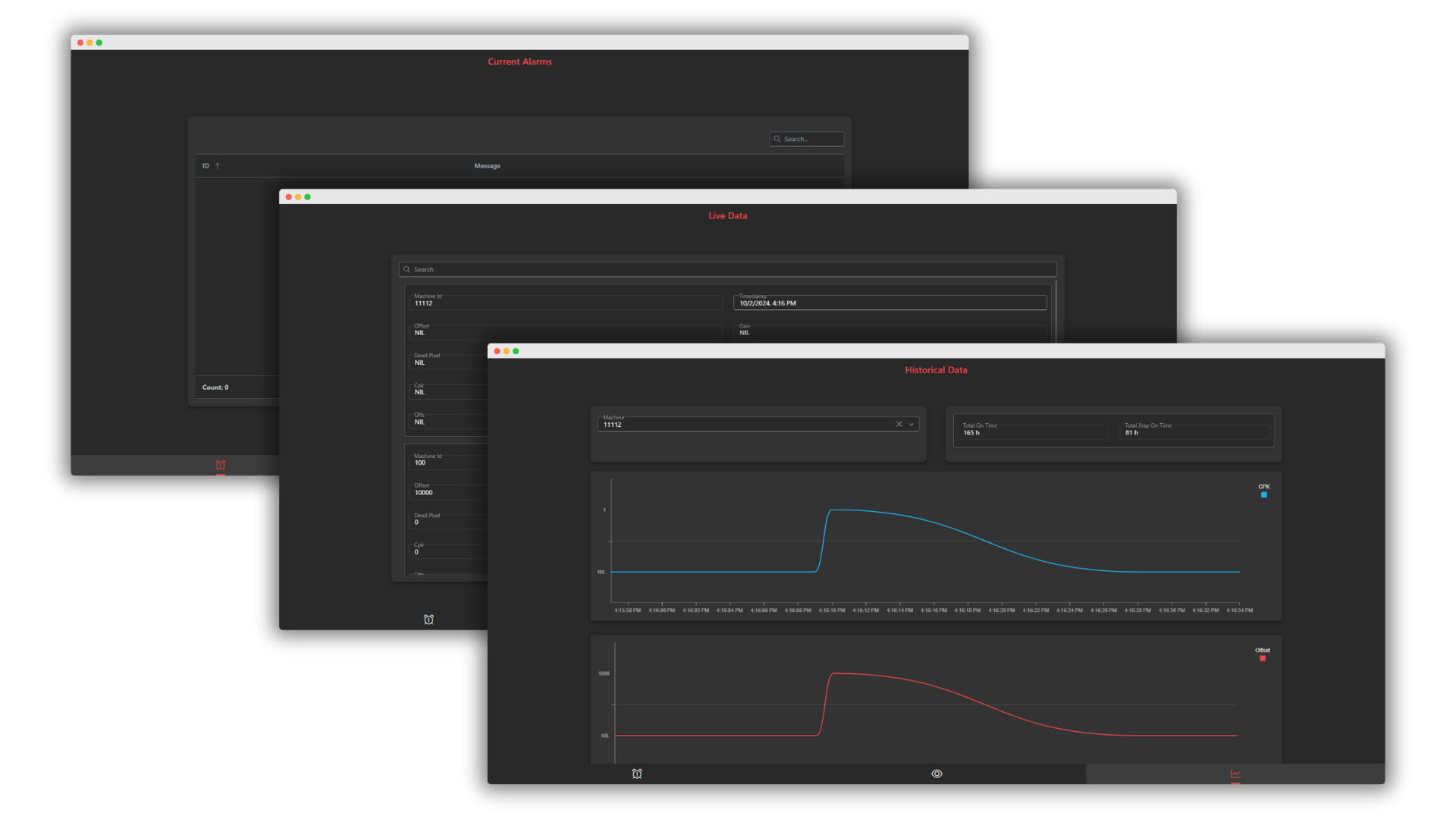
Easy Onboarding of New Machines
The Heisenware Agent can be installed on both new and existing machines without any customization. The same file is used across all machines. Thanks to a unique ID on each machine’s controller, incoming data is automatically assigned to the correct machine, making onboarding extremely simple.
After installation, the agent connects to the cloud automatically, and the service dashboard instantly updates to include the new machine—no manual input required. Potential offline phases are easily bridged, with missing data transmitted as soon as the connection is restored, ensuring nothing is lost.
With Heisenware, we were able to quickly and easily collect machine data. The cloud-based analysis within the low-code software has allowed us to optimize our service processes, boosting customer satisfaction. At the same time, the infrastructure we’ve built lays the foundation for further machine data-driven solutions.
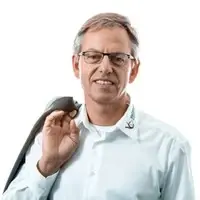
Optimized Service Process and Future-Proof Solutions for VisiConsult
VisiConsult’s service process has been significantly streamlined. Service technicians now have full, real-time access to machine data, allowing for faster identification of issues and immediate, targeted action. Automated data collection and transmission reduce manual effort and save valuable time previously spent on follow-up questions and tracking down details.
With the ease of onboarding new machines and seamless integration into existing control software, this solution is both scalable and future-proof. Plans are already in place to use the data for other applications, such as health monitoring. Looking ahead, these insights could also be made available to customers via dedicated apps. The groundwork for these developments is already in place.
Low-Code Machine Data Monitoring
Looking for an easy and affordable way to monitor and analyze your machine data? We’re here to help! Let’s find out together if Heisenware is the right solution for your needs.