HEDELIUS Boosts Efficiency Through Machine Connectivity and Seamless System Integration
HEDELIUS has implemented a tailored solution for digitally connecting its machine controls to the MES system. By using Heisenware, manual data entry was eliminated, and data flows were fully automated. This led to a significant increase in production efficiency, laying the groundwork for future Industry 4.0 projects—both within HEDELIUS and for their customers.
About HEDELIUS
HEDELIUS Maschinenfabrik GmbH, with around 250 employees, is a pioneer in developing and producing vertical CNC machining centers. The company offers innovative three-, four-, and five-axis machines along with automation solutions for single-part and small-batch production. Customers from industries such as special machinery manufacturing, aerospace, and automotive rely on the precision, stability, and reliability of HEDELIUS CNC machining centers.
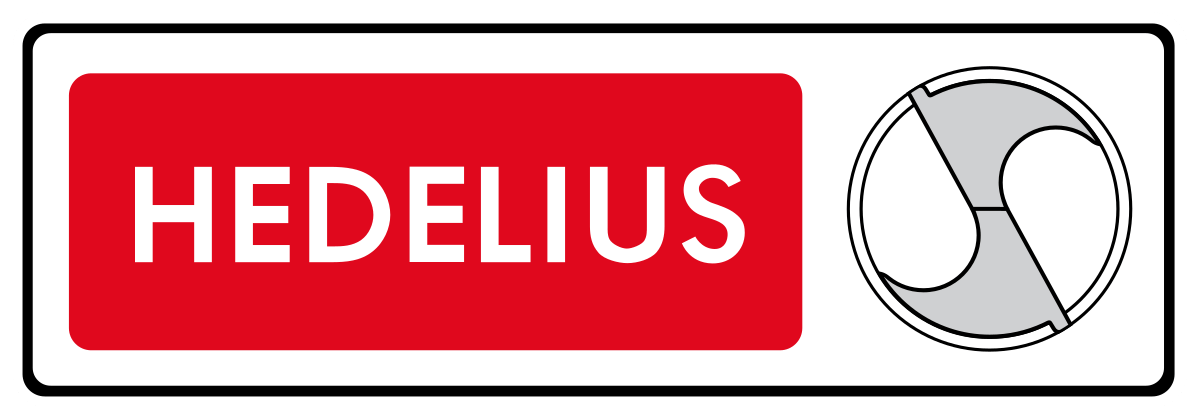
Heterogeneous Systems and Inefficient Machine Data Collection
HEDELIUS faced the challenge that data from its 11 CNC machines in production had to be mostly collected manually. This process was not only time-consuming but also prone to errors. Connecting the machines to the existing MES system was difficult, as many of the controls in use—especially Heidenhain systems—were not directly supported.
While about half of the machines were equipped with modern OPC UA interfaces, older machines relied on proprietary DNC interfaces, making integration even more challenging. This technological diversity posed significant hurdles for automating the production process. The primary goal of HEDELIUS with this digitalization project was to increase efficiency while also creating a blueprint for future Industry 4.0 initiatives—both internally and for their customers.
Seamless Connectivity Through Configurable Integrations
HEDELIUS opted for a custom solution built on Heisenware, which handles both the transmission of machine data to the MES and the flow of order data from the MES to the machine controls. Two separate low-code software applications were developed for this purpose. The first application captures machine data using OPC UA and DNC integrations and provides it through an integrated OPC UA server. The MES Hydra 8 can directly take this data from the OPC UA server for further processing.
The second application, developed with Heisenware, automates order processing. Task data, prepared by an employee at the MES terminal, is processed and delivered as a batch file for the Heidenhain Batch Process Manager, installed on some controls. For machines without automated task processing, the orders are sent directly to the machine controls as planned by the operator at the terminal. These two applications create a continuous, efficient interface between the machines and the MES, enabling seamless and error-free data collection and order processing.
.png?width=1920&height=1080&name=Schaubild%20Hedelius%20Projekt%20(1).png)
Cloud-Based Setup With Local System Integration
HEDELIUS decided to leverage the benefits of a cloud deployment of Heisenware, although the solution could also be run entirely on-premise. This presented specific challenges in implementation and deployment, as both the machine controls and the MES are local systems that needed to be seamlessly integrated.
The solution was to deploy Heisenware Agents locally, which run integrations, connectors, and the OPC UA server. At the same time, the entire solution, including the Agents, can be centrally configured from the cloud. This architecture provides a flexible, easily configurable solution that meets HEDELIUS' high security requirements while offering maximum adaptability.
The data connectors of the Heisenware platform are easy to configure. This significantly simplified the integration of the MES and machine controls for us.

Significant Efficiency Gains and Valuable Know-How for the Future
Through the Heisenware solution, HEDELIUS eliminated manual data collection at the machines, resulting in substantial time savings and fewer errors. The seamless integration of machine controls and the MES system automated data flows, making production processes more flexible and efficient.
Within just a few months, HEDELIUS established an end-to-end digital process, transmitting order data to the machines without any media interruptions and providing real-time feedback into the MES system. Along with the efficiency gains, HEDELIUS also acquired valuable digitalization know-how, serving as a foundation for future Industry 4.0 projects within the company and for their customers.
Efficient Machine Connectivity With Low-Code Software
Would you like to increase the efficiency of your production through digital connectivity? We’re happy to advise you and find out how Heisenware can meet your needs.